Ferramenta de Gestão e Análise de Riscos Hazop: Quais são as etapas de aplicação desse estudo?
Fale conosco
(11) 4226-2641Endereço
R. Santa Catarina, 40 - Sl. 303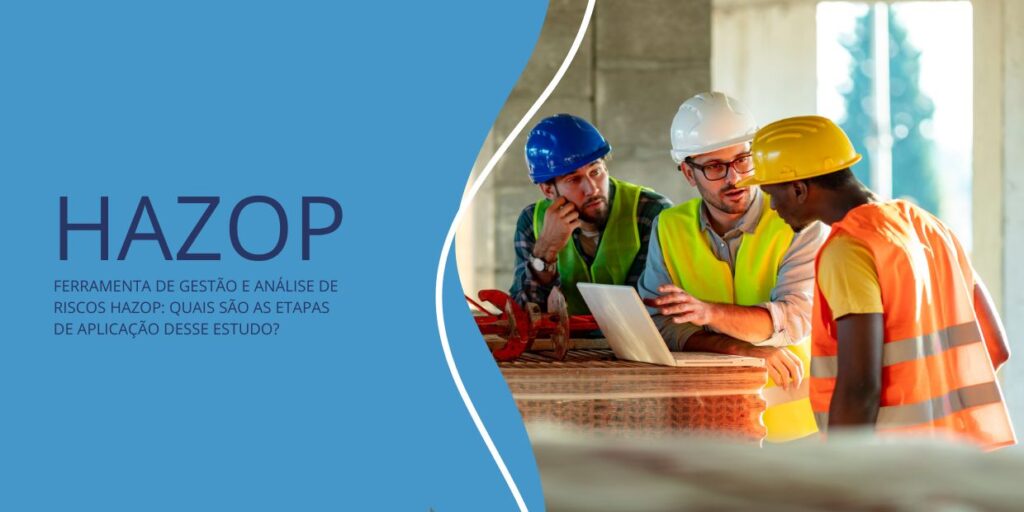
Por: Redator - 21 de Janeiro de 2025
Ferramenta de Gestão e Análise de Riscos Hazop: Quais são as etapas de aplicação desse estudo?
A gestão de riscos é uma prática essencial para garantir a segurança e a eficiência nas operações industriais. Uma das ferramentas mais eficazes nessa área é o Estudo de Perigos e Operabilidade (Hazop). Este artigo explora a aplicação do Hazop, suas razões, metodologias e a importância para a segurança do trabalho.
O que é o Hazop?
Hazop é uma técnica sistemática e estruturada de identificação e avaliação de riscos em processos industriais. Seu objetivo é examinar potenciais falhas e suas consequências, propondo medidas mitigadoras para garantir a segurança e a operabilidade das instalações.
Exemplos de razões para o estudo de Hazop
- Verificação de projeto: Avaliar a segurança e eficiência de um novo projeto.
- Decisão para construção ou não de planta industrial: Determinar a viabilidade de novos empreendimentos.
- Decisão para compra de equipamento: Garantir que novos equipamentos atendam aos padrões de segurança.
- Obtenção de lista de perguntas para fornecedor: Facilitar a comunicação de requisitos de segurança.
- Verificação de instruções de operação: Assegurar que os procedimentos operacionais estejam corretos e completos.
- Melhoria das condições de segurança da planta industrial: Identificar áreas para melhorias contínuas.
- Atendimento à exigência de órgão legislador de meio ambiente: Cumprir requisitos legais e regulatórios.
Definição sobre quais riscos devem ser avaliados
- Para o pessoal de operação da planta industrial: Identificação de riscos que possam afetar diretamente os trabalhadores.
- Para as instalações industriais: Avaliação dos perigos que possam comprometer a integridade das instalações.
- Para a qualidade do produto: Garantir que os riscos não afetem a qualidade final do produto.
- Para o público em geral: Prevenção de riscos que possam impactar a comunidade ao redor.
- Para o meio-ambiente: Identificação de perigos que possam causar danos ambientais.
Causas Básicas
- Falha humana: Erros operacionais ou de manutenção.
- Falha de equipamento: Quebras ou mau funcionamento de equipamentos.
- Eventos externos: Fatores externos como desastres naturais.
Probabilidade relativa da ocorrência
A probabilidade relativa da ocorrência de falhas é hierarquizada da seguinte forma:
- Falha humana > Falha de equipamentos > Eventos externos.
Parâmetros Operacionais (mais comumente empregados)
- Vazão
- Pressão
- Temperatura
- Nível
- Peso
- Composição
- Fase
- Densidade
- pH
- Viscosidade
- Velocidade
- Umidade
- Condutividade
Sugestão para membros de equipe para novos projetos
Recomendação: composição de 7 a 8 pessoas no máximo.
- Gerente do projeto (ou representante)
- Engenheiro de processo
- Engenheiro de controle e automação
- Engenheiro voltado a pesquisa e desenvolvimento
- Engenheiro eletricista
- Engenheiro de segurança
- Especialistas de meio ambiente, higiene industrial, reatividade química
- Líder de estudo
- Secretário
Sugestão para membros de equipe para plantas existentes
Recomendação: composição de 7 a 8 pessoas no máximo.
- Engenheiro chefe de operação
- Líder da operação
- Engenheiro de processo
- Engenheiro de manutenção
- Engenheiro de instrumentação
- Engenheiro de segurança
- Líder de estudo
- Secretário
Ações para gerenciar os perigos
As ações para gerenciar os perigos são geralmente de quatro tipos:
- Alteração do processo: Mudanças na receita, materiais, etc.
- Alteração nas condições do processo: Ajustes na pressão, temperatura, etc.
- Mudança nos procedimentos operacionais: Revisão e atualização de procedimentos.
- Alteração das condições de projeto: Modificações no design para melhorar a segurança.
Priorize as ações que removam as causas do perigo quando houver possibilidade, para então, analisar outras que reduzam as consequências.
Follow-up da Análise
O acompanhamento é essencial. Muitas causas ou consequências necessitam de informações adicionais de outros especialistas para compor as recomendações e muitos perigos identificados possuem ações que podem ou devem ser implementadas com alguma urgência.
São previstos uma frequência de até 2 reuniões por semana e devem ser de no máximo 3 a 4 horas. Dê preferência para as parciais da manhã para realizá-las.
Conclusão
A implementação do Hazop como ferramenta de gestão de riscos é vital para a segurança e a eficiência das operações industriais. Com a identificação sistemática de perigos e a adoção de medidas mitigadoras, é possível garantir um ambiente de trabalho seguro e conforme com as exigências regulatórias, protegendo trabalhadores, instalações, produtos e o meio ambiente.